Learning Light Weight Aluminum Spreading: a Deep Dive Into the Various Strategies Offered
From the traditional approach of sand casting to the complicated procedures of investment spreading and pass away casting, each strategy presents distinct challenges and benefits. In this exploration of aluminum spreading techniques, we will shed light on the intricacies of each method, giving understandings that might change your approach to aluminum casting.
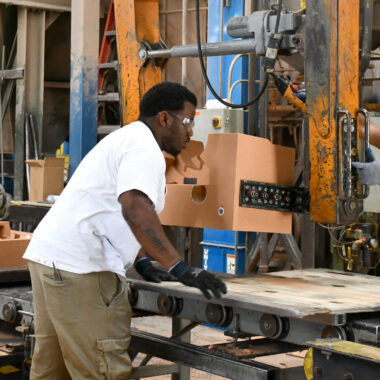
Sand Spreading Strategy Overview
The Sand Spreading technique's flexibility and extensive application make it a cornerstone in understanding aluminum casting processes. This strategy includes creating a mold and mildew from a blend of sand and a binder, such as clay, to develop elaborate shapes for casting molten light weight aluminum. Sand casting is a popular selection due to its reasonably affordable, simplicity of alteration, and capability to produce complicated geometries with high precision.
The process starts with the creation of a pattern, typically made from timber or steel, which is pushed into the sand to produce a mold and mildew tooth cavity. Once the pattern is gotten rid of, the mold dental caries is filled up with liquified aluminum, which strengthens to take the shape of the pattern. After cooling and solidification, the sand mold and mildew is damaged away, revealing the light weight aluminum casting.
Sand casting is commonly used in numerous industries, consisting of automotive, aerospace, and manufacturing, due to its adaptability in producing both huge and little aluminum components (aluminum casting). Its versatility to detailed designs and cost-effectiveness make it a favored choice for lots of light weight aluminum spreading applications
Permanent Mold And Mildew Casting Process Described
Exploring the ins and outs of light weight aluminum casting, the Long-term Mold Casting process offers a refined method for creating premium components with precision and efficiency. Unlike sand casting, permanent mold and mildew spreading makes use of a multiple-use mold and mildew usually made of steel or iron to shape the liquified light weight aluminum.
Long-term mold spreading can be classified right into 2 primary types: gravity casting and low-pressure spreading. Gravity spreading entails putting the molten steel right into the mold utilizing gravity, while low-pressure casting utilizes reduced pressure to fill the mold and mildew dental caries. Both techniques provide advantages in regards to lowering porosity and boosting mechanical residential or commercial properties.
Pass Away Casting: Benefits and Drawbacks
Mastering the intricacies of die spreading includes understanding its unique benefits and drawbacks in the realm of light weight aluminum element manufacturing. Die casting offers numerous benefits that make it a popular selection for generating light weight aluminum parts. One crucial advantage is the high-speed manufacturing capability of die casting, permitting the automation of complicated shapes with tight tolerances. In addition, pass away casting supplies excellent dimensional precision and smooth surface coatings, reducing the requirement for added machining procedures. The procedure is additionally extremely repeatable, making certain constant top quality throughout big manufacturing runs.
Nonetheless, die spreading does come with its very own collection of drawbacks. One major drawback is the high first tooling expense connected with producing the dies used in the process (aluminum casting). These molds can be pricey to create, making die casting less economical for tiny manufacturing runs. The procedure is not as adaptable when it comes to design adjustments contrasted to other casting techniques like sand casting. Regardless of these restrictions, the advantages of die spreading typically exceed the negative aspects, making it a favored option for lots of light weight aluminum spreading applications.
Financial Investment Casting Advantages and applications
Building on the advantages of die spreading, financial investment casting offers a functional method for producing detailed aluminum get redirected here components with one-of-a-kind advantages in various applications. Investment spreading, also referred to as lost-wax casting, excels in developing complicated forms that would certainly be impossible or hard to accomplish through various other methods. This technique is commonly used in markets such as aerospace, automotive, and fashion jewelry making.
One of the vital benefits of investment spreading is its capability to produce near-net form components, lessening the requirement for additional machining and decreasing product waste. This results in price savings and faster manufacturing times compared to typical machining processes. Furthermore, investment spreading enables the production of components with excellent surface area coatings and tight tolerances.
In the aerospace market, financial investment spreading is favored for its capability to generate lightweight yet strong elements vital for aircraft performance. The vehicle field benefits from financial investment spreading for producing elements with high dimensional precision and detailed styles. In general, investment casting provides a affordable and exact remedy for making intricate aluminum components throughout numerous sectors.

Lost Foam Casting: How It Functions
Lost foam spreading, likewise called evaporative-pattern casting, is an approach for producing detailed metal parts by making use of foam patterns that evaporate throughout the casting procedure. This method begins with a foam pattern of the preferred component being placed right into unbonded sand. The foam pattern is usually coated with a refractory material to enhance the surface coating of the final steel component. When molten metal is put into the mold and mildew, the foam evaporates due to the warmth, leaving behind a tooth cavity that is after that loaded by the metal.
One of the crucial benefits of lost foam spreading is its ability to create intricate forms with intricate information that may be challenging to accomplish with various other casting approaches. Additionally, the procedure can be cost-effective as it gets rid of the requirement for cores and enables for the combination of multiple elements into a single component. It needs cautious control of the process specifications to make certain proper foam vaporization and steel circulation.
Verdict
To conclude, understanding light weight aluminum casting involves understanding and using different methods such as sand spreading, image source long-term mold casting, pass away spreading, investment casting, and lost foam casting. Each technique has its very own benefits and applications in the manufacturing procedure. By acquainting oneself with these various approaches, makers can select the most ideal spreading strategy for their specific demands and demands, ultimately resulting in successful and reliable manufacturing of aluminum components.
From the traditional technique of sand spreading to the facility processes of investment spreading and die spreading, each strategy presents distinct challenges and i was reading this benefits. In this expedition of aluminum spreading strategies, we will drop light on the complexities of each approach, offering understandings that might reinvent your approach to light weight aluminum spreading.
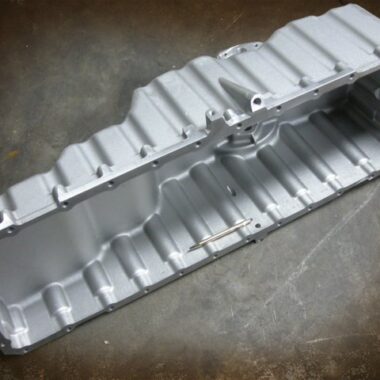